- صفحه نخست
- محصولات
سوزن
مجموعه دستگاهی که باعث هدایت قطار از مسیر مستقیم به مسیر انشعابی می شود.
اجزای سوزن
سوزن از مجموعه قطعات فورج شده، ریخته گری شده، ماشینکاری شده، جوشکاری شده و... تشکیل شده است.
سیستمهای اتصال
سیستم اتصال در سوزن متشکل از پیچ تراورس، انواع واشرهای فنری، پابندهای فنری و ... می باشد.
بافراستاپ
بافر استاپ وسیله ای است که در انتهای خطوط ریلی نصب میشود
- خدمات
- اخبار و مقالات
- پروژهها
- درباره ما
- تماس با ما
- همکاری با ایرید
- > اخبار و مقالات
- > اتصال غیر همجنس قطعه تکه مرکزی از جنس فولاد هادفیلد به قطعه ریل از جنس فولاد R260
اتصال غیر همجنس قطعه تکه مرکزی از جنس فولاد هادفیلد به قطعه ریل از جنس فولاد R260

محمّد متقی پور1، محمّد ملک آبادی2،صادق عبادی*3
1مدیر عامل شرکت گسترش صنایع ریلی ایران (ایرید)؛ Mottaghipour@iridco.ir
2 مدیر مهندسی و توسعه شرکت گسترش صنایع ریلی ایران (ایرید)؛ Malekabadi@iridco.ir
3* کارشناس ارشد تحقیق و توسعه شرکت گسترش صنایع ریلی ایران (ایرید)؛ Ebadi@iridco.ir
——————————–
چكيده
وجود درز و ناپیوستگی در خطوط ریلی همواره مشکلاتی را از لحاظ ایمنی و سهولت حمل و نقل به وجود آورده است به گونه ای که امکان افزایش سرعت عبور و مرور بر روی چنین خطوطی عملاً وجود ندارد. اغلب سوانح ریلی در محدوده سوزن که محل تغییر مسیر قطار از یک خط به خط دیگری است، رخ میدهد. سوزنهای ریلی از حدود 150 نوع قطعه ساخته میشوند که در بین آنها قطعه تکه مرکزی که به قلب سوزن نیز معروف است از اهمیت بالایی برخوردار است. تکه مرکزی منوبلوک یا یکپارچه به روش ریخته گری و از فولاد پرمنگنز یا هادفیلد ساخته میشود که می بایست ساختار آن به صورت کاملاً آستنیتی باشد. با توجه به اینکه در دماهای بالاتر از 250 درجه سانتیگراد در ریز ساختار این قطعه کاربیدهای مرز دانه ای ایجاد میشود جوشکاری این قطعه نیازمند تمهیدات و تجهیزات ویژهای است. همچنین در سمت دیگر این اتصال (جوش)، ریل از جنس فولاد کربنی R260 با ساختار کاملاً پرلیتی است که جوشکاری آن بایستی با استفاده از عملیات پیش گرم و در دمای بالا انجام گیرد. با توجه به اینکه جنس قطعات کاملاً متفاوت است، این اتصال در دسته بندی جوشکاری غیر همجنس میباشد و برای جوشکاری با توجه به هندسه جوش از روش جوشکاری شیار باریک الهام گرفته شده است. پژوهش حاضر به بررسی و مطالعه خواص این اتصال مطابق استاندارد EN 14587-3 میپردازد.
كلمات كليدي: اتصال غیر همجنس، تکه مرکزی، فولاد هادفیلد، فولاد ریل R260، جوشکاری شیار باریک.
————————————
مقدمه
خطوط حمل و نقل ریلی در حال توسعه به سمت استفاده از خطوط پر سرعت، بار سنگین و خطوط بدون درز است و از اینرو بهبود عمر کاری، خواص خستگی و مقاومت به سایش تقاطع های ریلی بیش از پیش مورد نیاز است. در سیستم های حمل و نقل ریلی در سرتاسر جهان، از ریلهای جوشکاری شده یکپارچه (CWRs[1]) به جای اتصالات مکانیکی (فیش پلیت[2]) استفاده میشود. عمده مزیت خطوط CWR، صرفه جویی اقتصادی و ضریب ایمنی بالا به خصوص در خطوط پر سرعت است. شماتیک سوزن ریلی در شکل (1) نشان داده شده است. یکی از اصلی ترین قطعاتی که در تقاطع های ریلی یا سوزنهای ریلی به کار گرفته میشود، تکه مرکزی یکپارچه[3] از جنس فولاد پرمنگنز معروف به فولاد هادفیلد[4] است. فولاد هادفیلد به موجب ماهیت ذاتی خود، هنگامی استفاده میشود که مقاومت به ضربات شدید و سایش بالا مورد نیاز است [1,2].
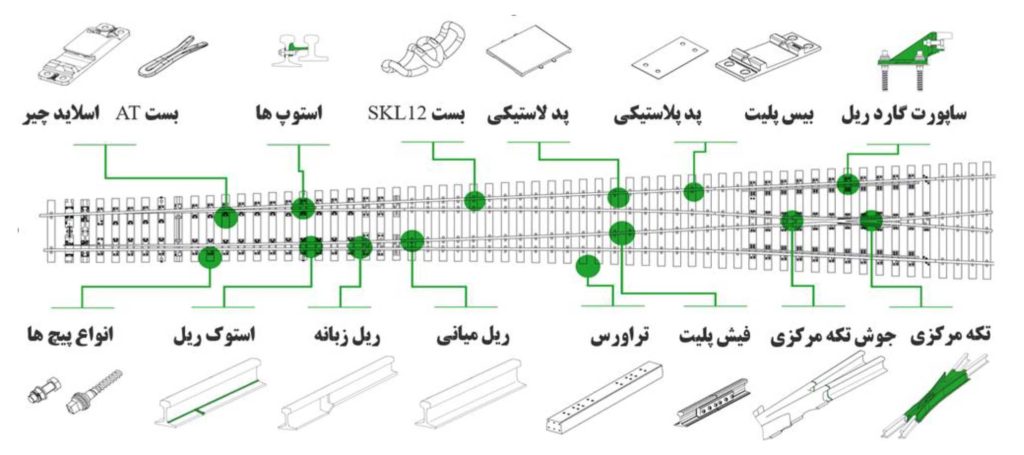
در حالت کلی، ترکیب شیمیایی فولاد هادفیلد که در خطوط ریلی و قطعه تکه مرکزی استفاده میشود در حدود 1% تا 1.2% کربن، %11 تا 14% منگنز و 0.3% تا 0.5% سیلیسیوم را شامل میشود. ریز ساختار آن در حالت ریخته شامل آستنیت و سمانتیت میشود. ریل های نورد شده با فولادهای R260 به کار رفته در خطوط ریلی تقریباً 0.6% کربن، 1.5% منگنز و کمتر از 0.5% سیلیسیوم در خود دارند. از اینرو، خواص مکانیکی و جوش پذیری متفاوت این دو ماده مشکلاتی را در فرایند جوشکاری به وجود میآورد. رسوب کاربید بر روی دانه های آستنیتی در منطقه متأثر از حرارت یا HAZ[1] فولاد هادفیلد، پارامترهای مکانیکی را کاهش داده و در آنِ واحد موجب کاهش خواص شکست به ویژه سختی، استحکام یا پلاستیسیته شکست میشود [3,4]. بر اساس استاندارد UIC 96/1692، تکه مرکزی مورد استفاده در خطوط ریلی بایستی به روش جوشکاری به ریل زبانه و ریل خط متصل شود. از روشهای رایجی که در اتصال ریل به ریل در احداث شبکه ریلی پیوسته (CWR) استفاده میشود، میتوان به روش
[1] Continuously welded rails
[2] Fishplate
[3] Monoblock Crossing
Hadfield [4]
[5] Heat-Affected Zone
روش های جوشکاری ترمیت[6]، جوشکاری گاز فشاری (GPW[7])، جوشکاری شیار باریک[8] و جوشکاری فلش بات[9] اشاره کرد. هنگام جوشکاری فولادهای پرمنگنز، دما همواره بایستی زیر 300 درجه سانتیگراد نگه داشته شود تا از رسوب کاربید که موجب ترد شدن فولاد هادفیلد هنگام جوشکاری میشود، جلوگیری گردد. از اینرو دما در محدوده 12 میلیمتری از حوالی منطقه جوش نباید از 250 درجه سانتیگراد فراتر رود [5,6]. روشهای جوشکاری ترمیت و گاز فشاری به دلیل عدم امکان جلوگیری از افزایش دمای تکه مرکزی به بالاتر از دمای 250 درجه سانتیگراد عملاً قابل استفاده نمی باشند.
این نکته مشهود است که با سریعتر شدن فرایند خنک کاری در جوشکاری، تشکیل کاربید کاهش مییابد؛ با این وجود از طرفی دیگر بر روی کیفیت جوش میتواند اثری معکوس داشته باشد. همچنین با افزایش سرعت خنک کاری فولاد پرلیتی در نزدیکی خط جوش، ساختار مارتنزیتی در خط ذوب به وجود می آید. با توجه به اینکه فاز مارتنزیت ترد است، انعطاف پذیری قطعه کاهش می یابد و از اینرو بایستی تنش زدایی شود. با توجه به مطالب ذکر شده، ترک سرد و حضور فازهای ترد در ناحیه متأثر از حرارت، از مهمترین چالشهای پیشرو در فرایند جوشکاری این نوع قطعات میباشند [7,8].
جوشکاری فلش بات یک نوع جوشکاری مقاومتی است که کنترل دما و همچنین کاهش منطقه متأثر از حرارت را امکانپذیر میسازد. در این روش از جوشکاری برای حل مشکل عدم جوش پذیری دو قطعه از یک قطعه واسط از جنس فولاد زنگ نزن استفاده میشود که قابلیت جوشکاری به هر دو قطعه از جنس فولاد پرمنگنز و فولاد ریل R260 را دارد. اولین بار یک فرد آمریکایی این روش جوشکاری را ابداع کرد [9]. در این پژوهش، قطعه واسطی از جنس فولاد زنگ نزن کم کربن آستنیتی استفاده شد. در سال 1991 یک مؤسسه استرالیایی در پژوهشی برای انجام این نوع اتصال از قطعه واسط فولاد زنگ نزن آستنیتی نیکل-کروم با پایدار کننده نیوبیم و تیتانیوم استفاده کرد که نتایج مطلوبی در پی داشت [10]. آلیسا و همکارانش [11] در پژوهش دیگری برای انجام این نوع از اتصال ابتدا روی سطح فولاد R260 پرلیتی را با فولاد زنگ نزن آستنیتی-فریتی پوشش داده و پس از آن جوشکاری بین دو قطعه را انجام دادند.
سینادسکی و همکاران [12] با انجام پژوهش بر روی جوش پذیری و اتصال فولادهای منگنزی و فولادهای کربنی به این نتیجه رسیدند که با استفاده از یک قطعه واسط از جنس فولاد آستنیتی کروم-نیکل میتوان این اتصال را به نحو مطلوبی به وجود آورد.
در حال حاضر روش فوق به عنوان تنها روش استانداردی است که در صنعت ریلی برای اتصال غیر همجنس قطعه تکه مرکزی از جنس فولاد هادفیلد به قطعه ریل از جنس فولاد R260 استفاده میشود. در پژوهش حاضر، با اقتباس از روش جوشکاری شیار باریک و با در نظر گرفتن تمهیداتی به منظور جلوگیری از افزایش دمای تکه مرکزی به بالاتر از 250 درجه سانتیگراد و کاهش منطقه متأثر از حرارت و انتخاب الکترودی مناسب به عنوان لایه واسط، قطعه تکه مرکزی از جنس فولاد هادفیلد به ریل از جنس فولاد R260 جوش داده شده است؛ نتایج به دست آمده از این روش جوشکاری با روش جوشکاری فلش بات مقایسه شده است. این نوع از جوشکاری برای اولین بار در ایران انجام شده و تا کنون سابقه ای از اجرای این روش در دیگر مناطق دنیا گزارش نشده است.
مواد و روش پژوهش
به منظور انجام این نوع از جوشکاری و انجام تست های مربوطه بر اساس استاندارد EN14587-3 که استاندارد مربوط به تست های جوشکاری فلش بات است، در ابتدا چندین قطعه از جنس فولاد هادفیلد و با پروفیل ریل به طول یک متر و با در نظر گرفتن 5 میلیمتر بار ماشین کاری ریخته گری شد. آنالیز شیمیایی این قطعات در جدول (1) ارائه شده است. بعد از ریخته گری قطعات، برای ایجاد پروفیل ریل UIC60 ماشینکاری و سنگزنی بر روی این قطعات انجام یافت.
[6] Thermit Welding
[7] Gas Pressure Welding
[8] Narrow-Gap Welding
[9] Flash-Butt Welding
چندین قطعه ریل UIC60 با جنس فولاد پرلیتی R260 به طول یک متر برش داده شدند. آنالیز شیمایی این قطعات نیز در جدول (1) ارائه شده است. برای انجام عملیات جوشکاری این قطعه ها روی یک فیکسچر مخصوص نصب شده و فاصله شیاری به اندازه 15 میلیمتر بین دو قطعه در نظر گرفته شد. فیکسچر مربوطه در شکل (2) نشان داده شده است.
فرایند جوشکاری با الکترودهای مخصوص و روش قوس الکتریکی و با رعایت عدم افزایش دمای قطعه تکه مرکزی با روشهای خنک کاری و همچنین کنترل دمای قطعه ریل از جنس فولاد R260 انجام یافت. پس از آن، آزمون ترک یابی مایع نافذ (PT) در کل منطقه جوش صورت پذیرفت. به منظور بررسی مقدار نفوذ جوش در فلز پایه و وجود عیوب احتمالی، ماکروگرافی نمونه ها انجام شد. برای این منظور، آماده سازی نمونه ها بر اساس استاندارد EN 14587-1 انجام یافته است. همچنین برای بررسی ریز ساختار و مطالعه فازهای موجود در مقطع عرضی جوش، متالوگرافی نمونه ها انجام یافت. آماده سازی نمونه ها برای این آزمون مطابق استاندارد ASTM E3-11 انجام یافت؛ تصاویر متالوگرافی نیز بر اساس استاندارد ASTM E883-11 تهیه شده اند؛ لازم به ذکر است در این آزمون از محلول نایتال 2 درصد استفاده شده است. بر روی نمونه های مذکور آزمون سختی سنجی ویکرز (HV30) با زمان اعمال نیروی 15 ثانیه در طول پروفیل و در 41 نقطه مختلف نیز انجام یافت.
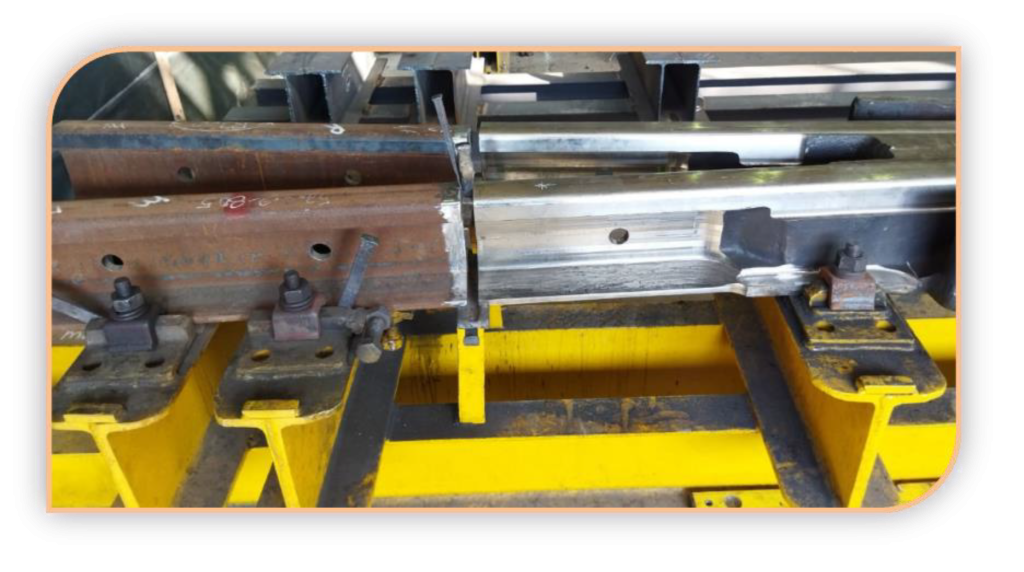
با توجه به ماهیت جنس قطعه تکه مرکزی که یک فلز کار سخت شونده است و همچنین موقعیت استفاده از این قطعه تحت بارهای خستگی و ضربات وارده از سمت چرخ قطار میتوان گفت که از مهمترین آزمونهای این قطعه آزمون خمش سه نقطه ای و آزمون خستگی میباشد که شرایط انجام این آزمونها مطابق استاندارد EN 14587-3 صورت پذیرفت.

نتايج و بحث
به منظور ارزیابی و اطمینان از ساختار محل اتصال قطعه تکه مرکزی به ریل R260، آزمون های ترک یابی مایع نافذ، رادیوگرافی، ماکروگرافی، متالوگرافی، سختی سنجی، خمش سه نقطه ای و آزمون خستگی مطابق استاندارد EN 14587-3 بر روی نمونه های آماده شده انجام یافتند که نتایج این آزمون در بخشهای بعدی ارائه شده اند.
آزمون ترک یابی مایع نافذ، PT
آزمون ترک یابی مایع نافذ به منظور بررسی عیوب سطحی و زیر سطحی که به سطح راه دارند و همچنین بررسی انواع ترکهای سطحی بر روی نمونه های جوشکاری شده انجام یافت و هیچگونه ترکی در نمونه ها مشاهده نشد. در شکل (3) تصاویر مربوط به این آزمون ارائه شده است. در تصویر (3-الف) اعمال مایع نافذ روی نمونه و در تصویر (3-ب) اعمال آشکارساز نشان داده شده است. با توجه به شکل (3-ب) مشاهده میشود که سطح قطعه کاملا سفید رنگ بوده و هیچگونه رنگ قرمزی که حاکی از عیوب ذکر شده باشد مشاهده نگردید. با توجه به اینکه این قطعه در شرایط کاری خود تحت بارهای خمشی و متناوب قرار میگیرد، از اینرو پای ریل (سطح زیرین ریل) تحت تنش کششی قرار خواهد گرفت و بنابراین در صورت وجود ترک در این ناحیه، احتمال باز شدن و گسترش ترک بالا است و اکثر شکستها از محل پای ریل رخ میدهد؛ این موضوع میتواند ریسک های زیادی را به ایمنی خطوط ریلی وارد سازد، بدین جهت این منطقه به دقت مورد بازرسی واقع گردیده تا از عدم وجود هرگونه ترک در این ناحیه اطمینان حاصل شود.
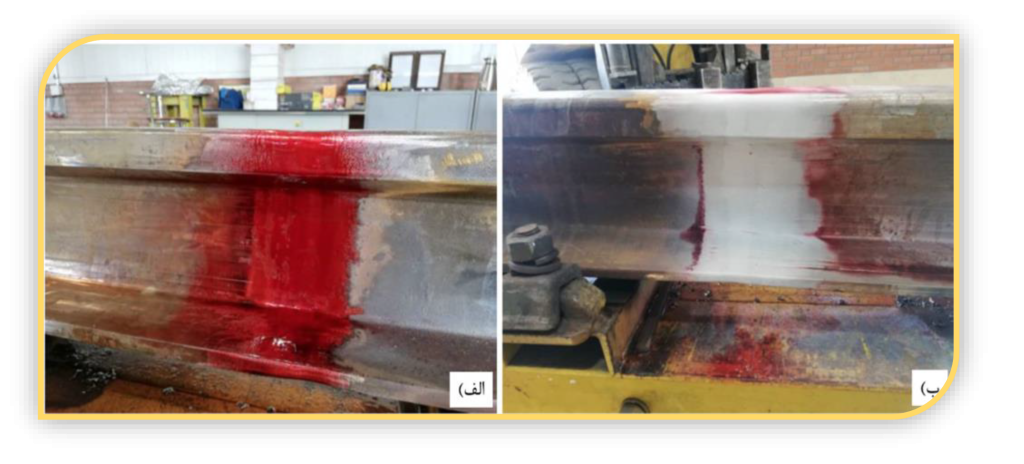
آزمون رادیوگرافی، RT
قطعه تکه مرکزی در طول عمر کاری خود تحت بارهای متناوب خستگی خواهد بود که این امر موجب گسترش عیوب داخلی به سطح قطعه و شکست آن خواهند شد. با توجه به روش جوشکاری مورد استفاده در این پژوهش، امکان وجود عیوب داخلی از قبیل ترک، آخال سرباره و مُک دور از انتظار نیست؛ از اینرو نمونه ها تحت آزمون رادیوگرافی قرار گرفتند. نتایج به دست آمده از این آزمون نشان داد که نمونه ها کاملاً سالم بوده و هیچگونه عیب داخلی اعم از ترک، آخال، مُک و … در ساختار نمونه ها وجود ندارد. نمونه ای از گزارش رادیو گرافی برای یکی از نمونه های جوشکاری شده در شکل (4) ارائه شده است.
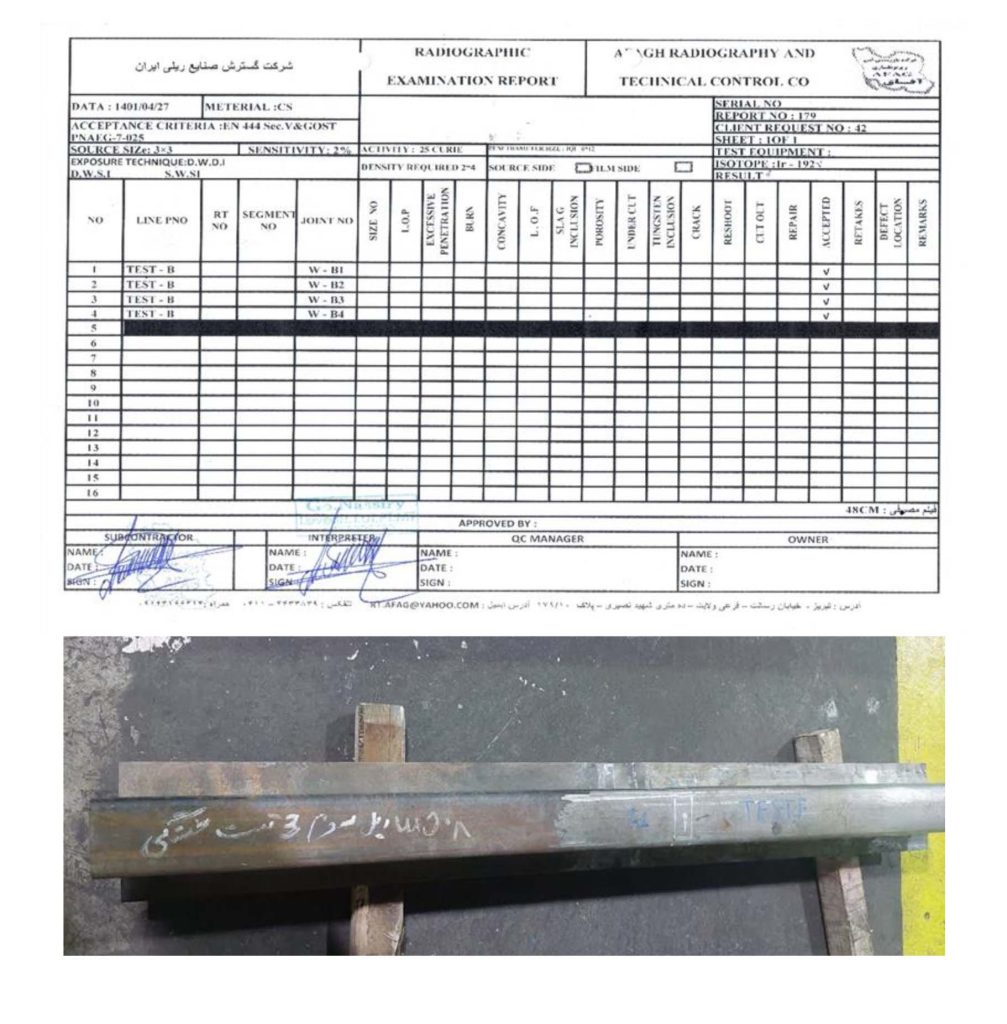
آزمون ماکروگرافی
تصویر ماکروگرافی انجام شده برای یکی از نمونه ها در شکل (5) ارائه شده است. بررسی تصاویر ماکروگرافی انجام شده نشان می دهد عرض منطقه متأثر از حرارت (HAZ) در حدود یک سانتیمتر می باشد. همچنین ریشه جوش، فلز جوش و منطقه متأثر از حرارت، عاری از هرگونه ترک، حفره گازی، ناخالصی سرباره و… می باشد. با توجه به اینکه عرض شیار قبل از انجام جوشکاری مقدار 15 میلیمتر در نظر گرفته شده است، میتوان از تصاویر ماکروگرافی نتیجه گرفت که نفوذ فلز جوش در هر کدام از فلزات پایه در حدود 3.5 میلیمتر است.

آزمون متالوگرافی
شکل (6) ناحیه اتصال فلز جوش به فلز هادفیلد را به تصویر کشیده است. از این رو با توجه به تصویر میتوان ملاحظه کرد که فولاد هادفیلد ساختار آستنیتی خود را به صورت کامل حفظ کرده است. در فصل مشترک فلز جوش و فولاد هادفیلد مقدار اندکی کاربید مرزدانه ای مشاهده شده است. با توجه به تمایل بالای ساختار فولاد هادفیلد برای تشکیل کاربید در دماهای بالای 250 درجه سانتیگراد و همچنین فرایند جوشکاری قوس الکتریکی (حرارت ورودی بالا) وجود این مقدار از کاربید در این قسمت از نمونه قابل توجیه است.
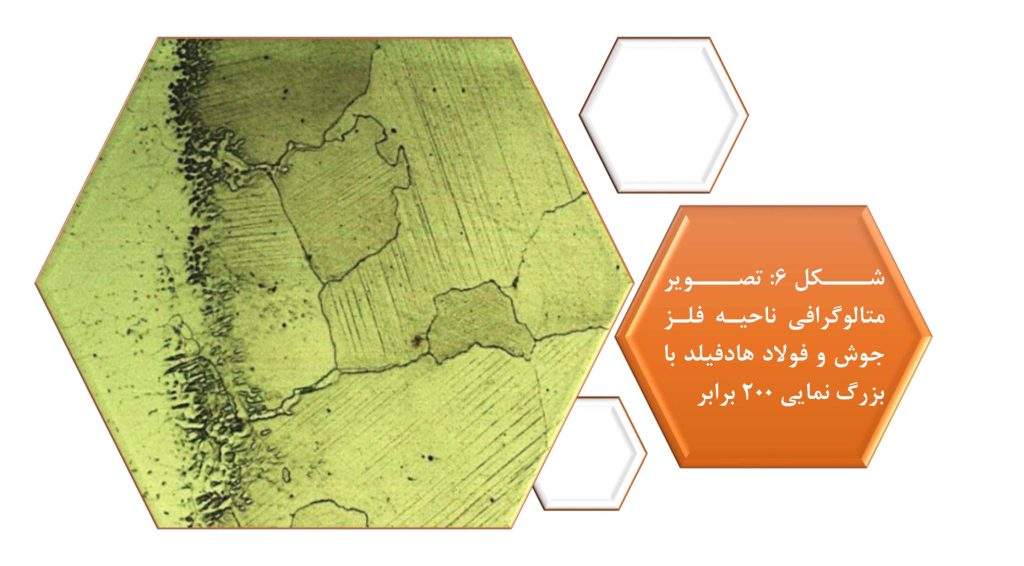
در شکل (7) که مربوط به اتصال فلز جوش به فولاد پرلیتی است، میتوان مشاهده نمود که ساختار کلی پرلیت است و مقداری فریت مرزدانه ای در نزدیکی ناحیه فصل مشترک اتصال دیده میشود. همچنین با توجه به مقدار بالای کربن در فولاد پرلیتی، عدم وجود فازهای کاربیدی و و ترد در ساختار میتواند دلیلی بر صحیح بودن انتخاب الکترود و فرایند جوشکاری باشد.
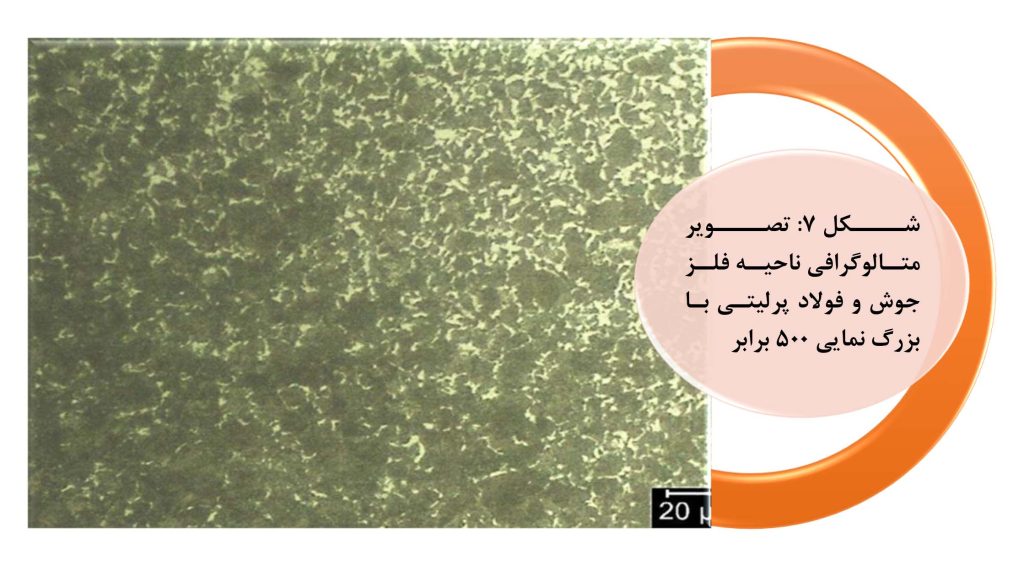
آزمون سختی سنجی
نتایج حاصل از سختی سنجی ریل با فولاد R260، فلز جوش و فولاد هادفیلد در شکل (8) ارائه شده است. با توجه به نمودار ارائه شده در این شکل، مشاهده میشود که متوسط سختی در ناحیه ریل از جنس فولاد R260 (فولاد پرلیتی) در حدود 275 ویکرز است؛ با نزدیک شدن به فلز جوش و ناحیه متأثر از حرارت (HAZ) سختی به مقدار تقریبی 255 ویکرز کاهش یافته است. در ادامه سختی فلز جوش در حدود 180 ویکرز اندازهگیری شد. با نزدیک شدن به ناحیه فولاد هادفیلد، سختی افزایش یافته و به مقدار سختی خود فولاد هادفیلد میرسد. طبیعی است که در مناطق متأثر از حرارت، با افزایش اندازه دانه ها نسبت به فلز پایه، سختی کاهش مییابد. روند منطقی افزایش و کاهش سختی در مناطق مختلف، حاکی از عدم وجود فازهای غیر تعادلی و صحیح بودن فرایند جوشکاری است.
آزمون خمش
قطعه تکه مرکزي در شرایط عملی و کارکرد در خطوط راه آهن همواره تحت بار خمشی متناوب میباشد به همین دلیل حساس ترین و مهمترین آزمون براي اطمینان از استحکام جوش شاخکهاي تکه مرکزي، آزمونهای خمش و خستگی هستند. با توجه به اینکه روش جوشکاري مورد استفاده در این پژوهش جايگزینی براي جوشکاري فلش بات است، براي آزمون خمش از شرایط ارائه شده در استانداردEN 14587-3 که مختص جوشکاري فلش بات است، استفاده شده است. شماتیک نحوه انجام این آزمون در شکل (9) ارائه شده است. مطابق استاندارد فوق الذکر، برای بررسی استحکام خمشی محل اتصال، بایستی آزمون خمش سه نقطه انجام شود به گونه ای که فاصله تکیه گاه ها از هم یک متر بوده و فک اعمال نیرو درست در مرکز خط جوش واقع شود. نتایج این آزمون نشان داد که قطعه جوشکاري شده قبل از شکست، نیروي 90 کیلو نیوتن و حداکثر خیز 21 میلیمتری را تحمل کرده است. با توجه به حد پذیرش استاندارد مذکور این قطعه مورد تأیید این استاندارد می باشد.
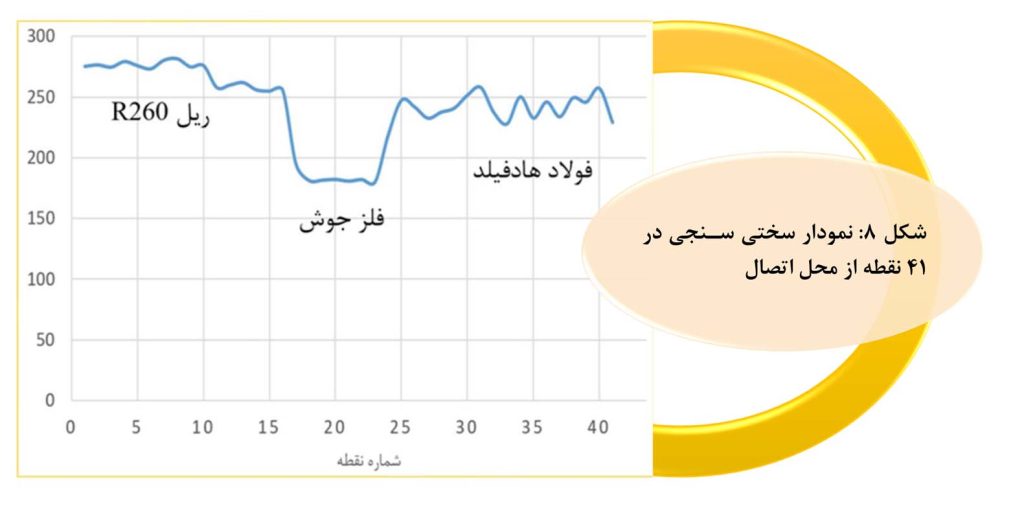
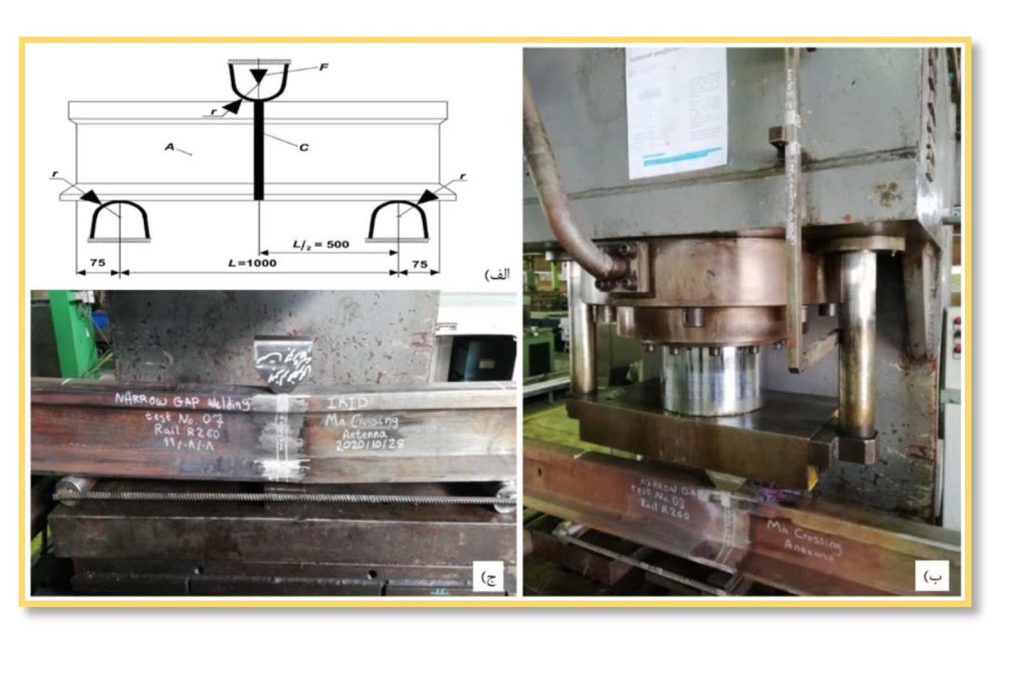
آزمون خستگی
یکی از آزمونهای با اهمیت به منظور اطمینان از صحّت اتصال غیر همجنس برقرار شده میان قطعه تکه مرکزی از جنس فولاد هادفیلد و ریل UIC60 از جنس فولاد R260 با توجه به ماهیت عملکردی قطعه که تحت بارهای رفت و برگشتی قرار میگیرد، آزمون خستگی است. از اینرو نمونه های آماده شده مطابق استاندارد EN 14587-3، به منظور بررسی عمر خستگی اتصال جوش، تحت آزمون خستگی خمش چهار نقطهای قرار گرفتند. آزمایش توسط دستگاه Amsler Universal Fatigue Test Machine ساخت شرکت Zwick آلمان انجام یافت. بر اساس استاندارد مذکور، نمونه ها بایستی تحت بارگذاری متناوب، تنش 130 MPa در دورترین تار از مقطع ریل در محل جوش را به تعداد 5 میلیون سیکل بارگذاری تحمل نمایند. با توجه به بازرسی چشمی و آزمون رادیوگرافی انجام یافته پس از آزمون خستگی، هیچگونه ترک و عیبی در قطعه مشاهده نگردید. دستگاه آزمون و فیکسچر طراحی و ساخته شده برای ایجاد تنش 130 MPa در محل جوش، در شکل (10) نشان داده شده اند.
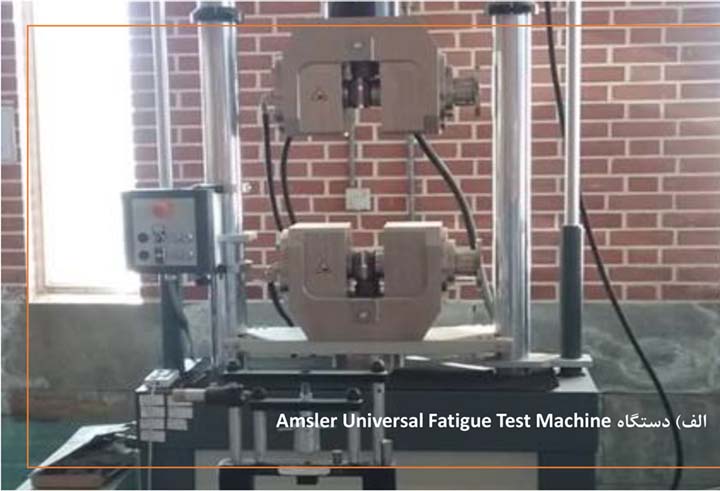
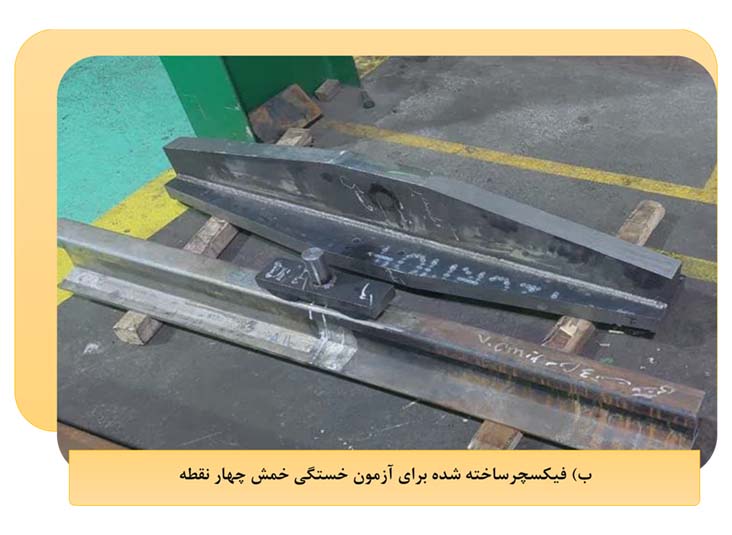
نتيجه گیری و جمع بندی
در این پژوهش اتصال غیر همجنس قطعه تکه مرکزی (مورد استفاده در سوزنهای ریلی) از جنس فولاد هادفیلد با قطعه ریل UIC60 از جنس فولاد R260 مورد مطالعه قرار گرفت. با توجه به نتایج مطلوب و قابل قبول به دست آمده از آزمونهای ترک یابی مایع نافذ، رادیوگرافی، ماکروگرافی، متالوگرافی، سختی سنجی، خمش سه نقطهای و آزمون خستگی مطابق استاندارد EN 14587-3، میتوان اینطور عنوان کرد که از این روش جوشکاری میتوان برای اتصال ایمن قطعه تکه مرکزی از جنس فولاد هادفیلد به ریلهای R260 مورد استفاده در خطوط ریلی استفاده کرد.
مراجع
[1] Ham, Y-S., Kim, J-T., Kwak, S-Y., Choi, J-K., Yoon, W-Y., “Critical cooling rate on carbide precipitation during quenching of austenitic manganese steel,” China Foundry, vol. 7, no. 2, pp. (May 2010).178‒182.
[2] H. S. Avery, ‘Austenitic Manganese Steel for Railway Track work’, Case report No 429-12, Abex Corporation Research Center, Mahwah, NJ 1981, p. 39.
[3] Mendez, J.; Ghoreshy, M.; Mackay, W. B. F.; Smith, T. J. N.; Smith,R.W. Weldability of Austenitic Manganese Steel. // Journal of Materials Processing Technology. 153-154, 1- 3(2004), pp. 596-602.
[4] Sevcikova, X.; Krejci, L.; Konecna, K. Mechanical and Corrosion Properties of Galvanic Coatings based on Zinc. // METAL 2013: 22nd International Conference on Metallurgy and Materials, pp. 1117-1122.
[5] Roll Crusher Maintenance, Rebuilding, and Repair, Pit and Quarry, October 1970, pp. 104 106.
[6] H.S. Avery, et al., Weld. J. 33 (5) (1954) 459–479.
[7] M. Neslusan, I. Mrkvica, P. Raos. ” Heat Distribution when Nickel Alloy Grinding.” Technical Gazette (2012): 947-951
[8] F. Zhang, B. Lv, B. Hu, Y.Li. ” Flash butt welding of high manganese steel crossing and carbon steel rail.” Materials Science and Engineering: A (2007): 288-292
[9] M. Alfred, H.J. Augustin, USA Patent, US4,169,745 (1977)
[10] J. Blumauer, USA Patent, US5,170,932 (1991)
[11] F. Pons, A.M.J. Spolidor, D.L. Seillier, USA Patent, US5,304,777A (1994)
[12] N A Sinadskii, L A Turbina, I Z Genkin, B E Glyuzberg, V M Dusevich, N V Bogorskii & N D Goronkov (1994) Welding high‐manganese and carbon steels, Welding International, 8:1, 58-6